Japanese Alloy Basics 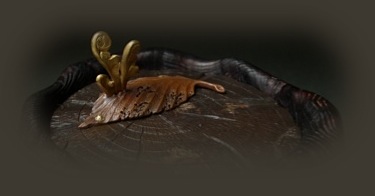
Alloys are melted mixtures of elemental metals such as copper, gold, silver, lead and tin. Japanese alloys are often binary(two metals), or tertiary(three), but can contain five or more metals. Metals are also used in their unalloyed, pure form, most often copper, silver and gold.
The two most esteemed Japanese alloys are shakudo and shibuichi. Shakudo is primarily copper with, most often, 3 to 6% gold but can be 10% or even more of gold. The gold content is varied to control the resulting shade of black-blue/black when treated in the traditional chemical bath.
Shibuichi is primarily copper and silver in varying proportions, again dependant on the color desired. The silver percentage can range from 2% to 60% or more, but more often would fall in the 15 to 40% range. These percentages are not haphazard, but are calculated for a specific color result based on centuries of experience. Shibuichi patinated with the traditional Japanese irotsuke technique offers a wide range of grays with some browns when using very low silver content. Pure gold and silver are not affected by the irotsuke chemical patination so retain their natural raw colors.
The metal artist works his chosen alloys into a creation depending on his color scheme. The alloys are incorporated using various inlay and overlay techniques and are further worked by carving, engraving, chasing and polishing.
After the final polishing, the last step is the revelation of the colors through the patination process, a specific chemical boiling bath. Each individual alloy reacts uniquely with this treatment, developing it’s own color. Small variations in the metal alloy percentages make subtle variations in the final colors. (see link to patination tutorial above; click "Tutorials")
One of the treasures I brought back from my first trip to Japan in 1987 was an alloy/patination chart that was given to me by Prof. Hiramatsu (now retired) at Tokyo Geidai(University of Fine Arts) metals dept. I've handed this out over the years and would like to make it freely available. You can download a PDFcopy HERE
In many ways it prompts as many questions as it answers, but that seems to be the nature of the beast. At least I'm certain the information it gives is accurate as it comes from the tradition of Kano Natsuo and Unno Shomin who taught at Geidai. I was told that it was prepared some years ago by a Professor Sakae Kimio for a workshop he had prepared(I think to be given in Australia).
There are several points to make.
I would advise against using kuromido as it contains arsenic.
This chart, useful as it is, does not cover many other interesting and useful alloys, including the bronze and brass(shinchu) groups.
It offers much though to those interested in a practical entry into Japanese alloys.
All of the colors referred to assume the use of the traditional patination with formula as given in the chart.
I would not pay too much attention to the qualifier "good", especially as it applies to shibuichi. In my experience the percentages used in alloys are to obtain specific colors and beyond that, there isn't any particular reason to say one alloy is "better" than another. So pertaining to shibuichi, the four alloys given should, in my opinion, be only viewed as a guide to range of color. Essentially any percentage ratio of the binary silver/copper will yield a specific color, with the colors getting darker as there is more copper present. "Nami" shibuichi means common or ordinary. I think the usefulness of any silver content above 60% is about nil.
It may be that the "good" qualifiers indicate a somewhat standard alloy that would serve the beginning alloyist well. I would concur.
The addition of gold in the "kuro shibuichi" group achieves very nice dark material.
The alloy formulae are given in parts by weight (except yamagane in percentages). This may be unfamiliar but isn't that hard to convert to percentages if desired.
In the PDF chart all information in b&w is original and I've added bits of information indicated in red.
Other information on alloys and technique at The Carving Path
|